With a series of innovations in the sustainable packaging field, Sirmax Group is making its debut at interpack, the international trade show for packaging machinery and products to be held in Düsseldorf from 4 to 10 May. The Italian manufacturer of engineering polymers, polypropylene-based compounds, post-consumer and bio-based materials is presenting to the public the novelties of two of its growing divisions: bio-based plastics and recycled plastics.
BioComp compostable bioplastics are completely biodegradable and compostable (they can therefore be disposed of in the organic fraction collection), with physico-mechanical characteristics that make them suitable for use in various sectors as a substitute for traditional plastics such as polyethylene, polypropylene and polystyrene, with the added advantage of being bio-based by nature, given their composition, which is obtained from vegetable biomass. The compound obtained from post-consumer materials (urban waste collection) is intended for the production of recycled HDPE pellets and thermoplastic pellets from recycled polypropylene, which are then used as "upgraded" raw materials for the production of compounds for durable goods.
Within the BioComp family, the company has developed and optimised new formulations specifically for injection moulding and extrusion, both of finished products and of sheets for thermoforming. The bio-compostable granulate is intended for the production of plates, cutlery, glasses, trays and, in general, anything related to rigid food packaging that can be disposed of together with the organic fraction of wet waste. The same material, specially modified, is also available in an injection-moulded version, suitable, for example, for the production of coffee capsules. These materials are known commercially by the abbreviation 'IM'. Also in view of the recent European regulations on coffee capsules, most of which are now made of aluminium or traditional plastic, the Padua-based group has developed a solution that, in addition to the material for the rigid part of the capsule, with mechanical and thermal characteristics suitable for withstanding high temperatures, also provides a material for the "barrier film", i.e. the flexible part that covers the capsule and comes into contact with the food.
In general, the historical products of the Biocomp range, through their "BF" codes, cover a wide range of applications in the flexible packaging sector and are therefore suitable for blown film extrusion for fruit and vegetable bags, organic fraction collection and various other types. All BioComp brand products are also UNI EN 13432 compliant and can boast the "OK Compost Industrial" certification and, for some grades, the more stringent "OK Compost Home" certification. This is the context of the new dog excrement bags produced by BioSave PlasticFree, a start-up company based in Gubbio (Perugia), using Sirmax bioplastic. The BioSave PlasticFree bags are fully recyclable, 100% compostable and UNI EN 13432 certified as "OK Compost Home". It is a unique product that complies with the European directives on the reduction of waste by disposing of this type of waste in wet organic waste.

This product will also be on show at our stand, and we will be distributing a free sample to all visitors thanks to a 100% green kit specially created for the event,
explained Alberto Zanon, Sales Director Biocomp of the Sirmax Group.
Along with this novelty, we will be presenting a wide range of specific grades dedicated to packaging films with the OK Compost Home certification, that is, directly disposable, again with the organic fraction, in home composting systems. The Sirmax Group's research supports its partners and customers not only in the design of new products, but also in the formulation of increasingly greener and better performing plastics, with a view to reducing waste, increasing recyclability and reducing environmental impact.
We are delighted to be able to work with the Sirmax Group for the realisation of this product of ours, which is currently unique on the Italian market, certified according to the most stringent regulations and 100% made in Italy,
added Gabriele Lepri, CEO of BioSave.
In fact, in this sector, we have noticed that the main competition comes from companies in the Far East that are unable to guarantee the same quality and therefore market products that are declared sustainable but lack any official certification.
At Interpack, Sirmax Group will also present a 100% post-consumer recycled compound for the detergent sector. This granulate is intended for "bottle-to-bottle" production, i.e. the manufacture of bottles, flacons and canisters for household cleaning, personal care or building products from virgin plastic bottles and containers designed for the same purpose. Sirmax's initiative is based on a specific market need: today, bottle-to-bottle production is mainly based on blends of recycled and virgin plastic. Sirmax aims to go "bottle-to-bottle" using only 100% post-consumer plastic of a higher quality, producing a material suitable for blow moulding.
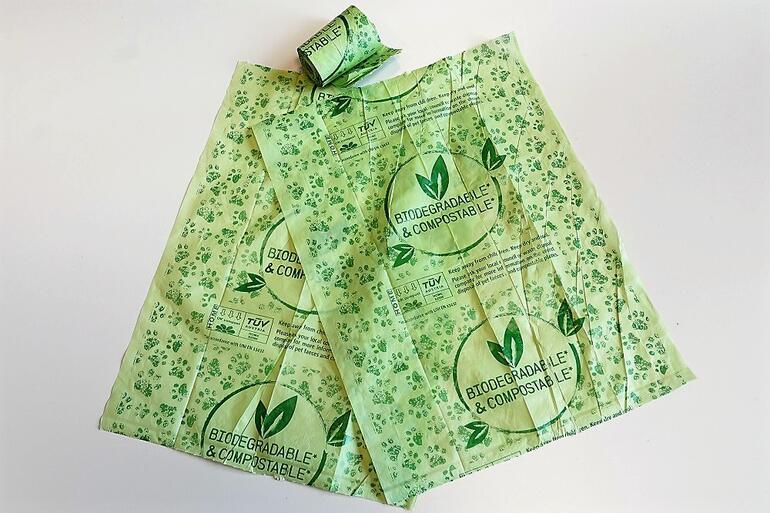
Mauro Zurlo, sales director Recycling di Sirmax Group commented:
Sirmax is adding a new element to the packaging sector by providing a sustainable material for the detergent sector that can be a viable alternative to virgin material. This is also upcycling, i.e. sustainability that is not just recycling, but the reuse of objects to create a higher quality product.
After Interpack, Sirmax will repeat the offer of the same products at PRSE (Plastics Recycling Show Europe), an exhibition dedicated to plastics recycling, to be held in Amsterdam on 10 and 11 May.