The second in a series of webinars was held on December 1st 2021, dedicated to new technologies that contribute to making plastics sustainable. The webinars acquaint visitors and exhibitors with GreenPlast in the lead-up to the first edition of the exhibition-conference scheduled for 3rd-6th May 2022 at the Fiera Milano fairgrounds in Rho-Pero.
This second appointment (the first took place on 9th and 10th November with the participation of Tomra, Previero, and Bandera), titled “Extrusion in plastics and rubber recycling processes”, witnessed the participation of more than one hundred companies, with three historical manufacturers of recycling lines for plastics and rubber taking the podium.
The first presentation, titled “Advanced plastics recycling using a co-rotating twin-screw extruder”, was delivered by Corrado Moneta, Technical Sales Manager of ICMA San Giorgio, a Lombardy company that has been in business since 1945. It has been specialized in plastics recycling since the mid-1980s and is now a leader in the production of twin-screw extruders and extrusion and compounding lines.
The speaker began by describing the three steps in recycling-compounding, blending, and devolatilization-and then focused on the advanced recycling phase, when additives are introduced into a twin-screw extrusion process to improve final product quality.
The second presentation was by Marco Girotto, R&D Technical Project Manager for Maris, a Turin-based company specialized in the production of co-rotating twin-screw extruders. His talk was titled “Evorec: advanced solutions for plastics and rubber recycling”. He discussed certain features of the Evorec (Evolved Recycling) technology, describing a co-rotating twin-screw extruder equipped with a dynamic mixer, which is able to process any free flowing material-both post-consumer and post-industrial-with certain parameters, such as low contaminant and moisture content.
In the second part of the presentation, Girotto illustrated the Evorec Plastic Plus technology, which uses a single-screw extruder connected to a co-rotating twin-screw extruder. This process makes it possible to convert highly contaminated materials, introducing additives to produce finished materials with high quality physical properties and a reduction in any inks present, while also reducing energy consumption.
The third and last presentation was by Marco Masiero, Test Engineer for Bausano, a Piedmont company that designs and produces plastics extrusion lines. Titled “Extrusion and Energy Savings: a winning combination for post-consumer plastics recovery”, it illustrated the strategy implemented by Bausano to respond to the demands of a circular economy, introducing energy efficiency systems on post-consumer reprocessing lines for materials such as PVC, HDPE, LDPE, and PP.
Specifically, the company designs and produces single- and twin-screw extruders for plastics recycling, both of which can be used for post-consumer materials while saving energy. The Smart Energy project, which heats the cylinder by induction, ensures energy savings of 35%. The cylinder is wrapped in an electrical coil which produces eddy currents that heat the cylinder. The advantages of this technology are: rapid cylinder heating, reduced electricity costs, and higher temperatures than can be achieved in traditionally heated cylinders.
The English version of the webinar was streamed live on 2 December at 10:30 am. The next event will take place in January 2022.
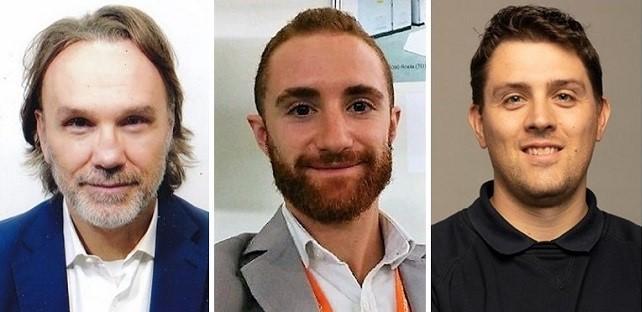