In order to make the production process in the plastic injection moulding industry more efficient, it is essential to reduce cycle time. Optimised cycle time results in specific and measurable benefits, such as increased productivity and, for the same number of parts, reduced operating costs and lower energy consumption. These benefits lead to greater production flexibility, essential for responding more quickly to changes in demand and remaining competitive in the market.
Thermal Care, part of Piovan Group (Italian multinational company operating in the development and production of automation systems for the storage, transportation and processing of polymers) has recently introduced to the market the Easytherm Flow series, designed to significantly improve the temperature control process. It works with a pressurised circuit up to 140°C and is equipped with multi-stage pumps that can reach flow rates of 300 l/min or maximum heads of 130 m. In addition, pump frequency control via an inverter allows the flow rate and head in the circuit to be varied to maximise performance (moulding cycle) and optimise energy consumption, operating around the point of best performance. Easytherm Flow can be customised with the main communication interfaces, including OPC-UA.
Reducing mould heating time, extracting heat quickly and maintaining a constant temperature throughout the entire production process are goals within everyone's reach with Easytherm Flow.
Minimisation of both cycle time and mould start-up time
1) Mould heating up to 20% faster than with a conventional temperature controller
It has been observed that by properly adjusting the frequency of the inverter, mould heating times can be reduced by up to 20%. This implies a significant decrease in start-up time, which is particularly advantageous for production runs that require frequent mould changes.
2) Rapid heat extraction guaranteed by the turbulent regime
The set point temperature can be easily set via the temperature controller's HMI, which also allows the flow, return, and mould temperatures to be monitored. Furthermore, by equipping the temperature controller with a flow meter, it is also possible to control the flow or return pressure and flow rate of the circuit.
The inverter maximises performance during the moulding cycle by optimising the flow rate and head in the circuit. It also minimises energy consumption by working around the best performance point of the multistage pump.
Temperature constancy during the entire production process
The decrease in the temperature difference between the supply and return lines enables a more uniform temperature distribution over the mould. This guarantees the highest quality of moulded parts, avoiding the problems arising from temperature variations from the set point, thus also reducing the production of rejects.
Switching to Easytherm Flow is a smart investment to increase production flexibility, starting a path to higher productivity, energy savings and superior moulded part quality.
For further information: https://www.piovan.com/product/easytherm-flow
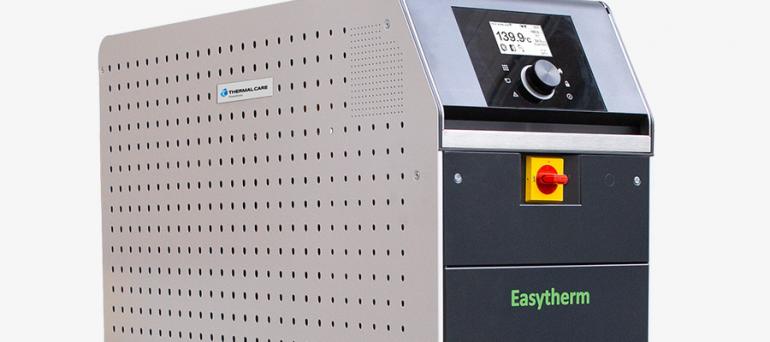