On June 14, Austrian injection-moulding machine manufacturer Engel held its usual press conference for journalists from around the world, to unveil its latest developments ahead of K 2022 (Düsseldorf, 19-26 October). The press conference took place at the company’s headquarters in Schwertberg (Austria), where it has a workforce of around 2 thousand employees.
Energy efficiency, the circular economy and digitalisation: these were the key topics dealt with by Engel. In the wake of two years in which it was forced to slow down the pace of its operations, the Austrian manufacturer was able to send out positive and encouraging messages for the future, thanks in part to the 375 million euro it has invested in recent years. In fact, the company’s production activity and projects have never stopped, and the multinational has continued to focus on the objectives and development plans that have allowed it to overcome the crisis in the automotive sector as well as the pandemic, maintaining a healthy order book. Its recovery is confirmed by the figures for the two-year period 2021-2022, during which Engel, which employs 7 thousand people globally, saw its turnover increase by 36% compared with the 2020 figure, reaching a peak of 1.5 billion euro. It is therefore now back to a level only slightly lower than for the two-year period 2018-2019, and has thus confirmed its leadership in Europe.
Engel produces injection-moulding machines at a rate of 60 a week. Many of them are used in the production of food packaging, one of the strategic application sectors of particular interest to this Austrian giant. The circular economy and the increasingly sophisticated demands of consumers, driven by continuous and hefty promotion of sustainability, as well as increasingly stringent European regulations, are in fact among the reasons why there is now a growing need, both for processors and for machinery manufacturers, to improve the production of packaging, to make it more competitive. Engel’s new Packaging Center - opened in mid-May with the aim of putting the company’s expertise in packaging production processes at the disposal of its customers - is part of this scenario.
Under the terms of the European Plastics Pact, by 2025 all packaging will have to contain at least 30% recycled material and be 100% recyclable. In this regard, driven by the demand for increasingly attractive and functional solutions, and the growing popularity of single-portion take-away foods, thin-wall packaging is expanding on a large scale, to the point of accounting for 12% of global packaging production. And in fact, the huge technological progress made by Engel concerns precisely this type of packaging. The materials used for thin-wall packaging are PP, PS and PET. The latter can be recycled indefinitely, and is therefore an advantageous solution for packaging manufacturers, allowing them to avoid being sanctioned by the European Union under the “Fit for 55” package of proposals, designed to bring in new, updated EU regulations concerning the green transition, and achieve climate neutrality by 2050. Therefore, although the price of PET is higher than that of other materials, such as PP, its recyclability makes it an economical choice. Furthermore, the European Food Safety Authority (EFSA), the agency which deals with food safety in the EU, has approved numerous PET recycling processes, also ensuring availability of the material in Europe.
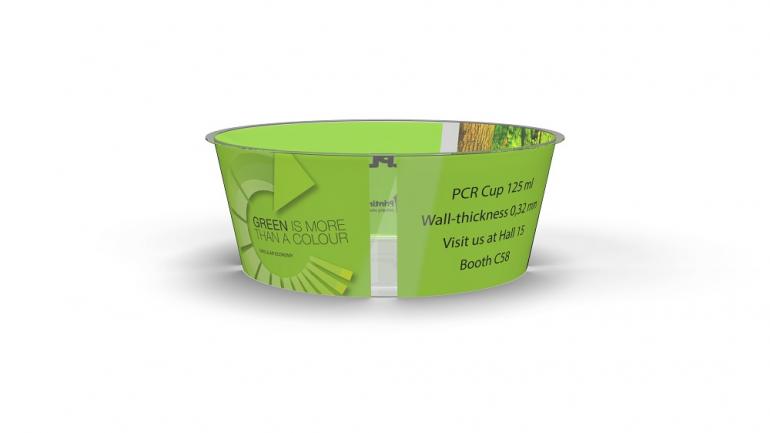
In this setting, Engel has entered into a collaboration with Alpla Group (an Austrian processor), Brink (a Dutch company specialising in in-mould labeling), and IPB Printing (a Dutch label printing company) to produce, in a single injection-moulding process step, thin-wall containers in rPET (obtained from drinks bottles), using E-Speed 280/50, a hybrid injection-moulding machine with an electrical clamping unit and a hydraulic injection unit for moulding 125-ml containers with a thickness of 0.32 mm, which are the kind typically found in the food industry. Furthermore, with this solution it is also possible to process recycled materials that contain up to 100% rPET, at speeds of up to 1,400 mm per second and injection pressures of up to 2,600 bar.
One of the main topics covered at the press conference was the increase in energy prices, which has prompted Engel to offer its customers tailor-made products in order to reduce their energy consumption. These efficiency packages include temperature control solutions coupled with intelligent assistance systems, applicable starting with the CC300 generation of control units.
The forthcoming K fair in Düsseldorf will be an opportunity to explore these and other new developments from the Austrian manufacturer.