An Italian producer of plastic films for flexible packaging, Ticinoplast, recently launched a web event entitled “Ticinoplast Partners Webinar: Sustainable Solutions for Packaging” with three other companies as protagonists - Novamont, Sun Chemical Group and Uteco Group - with which Ticinoplast cooperates to provide eco-sustainable solutions for a constantly evolving sector such as that of food packaging.
Below are some important themes that emerged during the discussions between the representatives of the four companies.
Mono-material PE solution
The webinar drew the attention in particular to the creation of a 100% polyethylene mono-material laminate suitable for different applications, with the aim of facilitating recyclability and pursuing the goal of an increasingly circular economy. In particular, the focus was on BOPE, a tenter-frame type bi-oriented polyethylene film which provides good mechanical and optical properties, suitable for printing and coating processes in single-layer and multilayer applications.
In this context, the BOPE PEoneer project has been developed thanks to the cooperation between Ticinoplast and Plastchim-T. Ticinoplast provides technological know-how and production supervision as the essential elements to deliver the best and widest range of BOPE films. In addition, the PEoneer project involves raw material suppliers, manufacturers of printing and laminating machines as well as packaging machines, producers of adhesives and coatings, as well as numerous processors in order to monitor the development and use of this new product range.
BOPE is an extremely innovative film, made from a mixture of high density and low linear polyethylene, which gives the material brilliance and transparency properties typical of other polymers, as well as mechanical characteristics that optimize processes, ensuring excellent printing and packaging results.
This film is also suitable for finishing processes, such as metallization and lacquering, that enhance its barrier properties. For the weldable substrate, Ticinoplast extrudes a bubble film specially designed to be laminated to the BOPE film and designed to guarantee standard performance during the packaging process thanks to its extremely low welding temperature. In this case, Uteco uses its Diamond HP mod. 112, particularly versatile and accurate, and the innovative technology of the DuaLam solventless coating and laminating machine, which guarantees output rates up to 35% higher for short runs, better than a traditional machine, as well as a more sustainable process.
Uteco's Dualam solventless laminating machine is characterized by an innovative lamination system that makes the machine suitable for applying high-performance solvent-free bi-component adhesives at a speed of up to 500 m/min and with curing times reduced by over 90%. Sun Chemical’s water-based inks from the Aqualam range were selected for internal printing. These inks are designed for the high-speed printing of plastic lamination films. The two films are laminated using the DuaLam lamination technology which - thanks to dedicated adhesives (DuaLam DCI017A and DCO005), characterized by rapid curing and high wettability - reduces significantly the non-polymer sections of the structure itself, with the aim of improving the recyclability and the quality of the recycled material obtained from end-of-life packaging. The DuaLam lamination technology also offers the advantage of a wide flexibility of use, also allowing the use of traditional adhesives depending on the performance of the final structure as well as on the desired characteristics.
Mono-material BOPE solution
As part of the BOPE PEoneer project, Ticinoplast has made available its extensive knowledge in the production of PE films, in terms of design, structure and formulations. The project also involves suppliers of raw materials, manufacturers of laminating and printing machines, producers of adhesives/barrier coatings and several converters, with the main aim of developing and bringing to the market sustainable solutions pursuing the philosophy of circular economy.
A BOPE film entails several benefits: it is designed for recyclability, so it facilitates PE mono-material structures, making the packaging easier to recycle and, at the same time, allows reuse in food packaging; has a high degree of processability and reliability; in other words, it features good flatness and printability, high mechanical and sealing properties, as well as excellent weldability to prevent leakage and reduce food waste; moreover, in terms of economy and performance, it offers the opportunity to downgauge the packaging without affecting its performance.
Compostable solution
The cooperation between Novamont, Ticinoplast, Sun Chemical and Uteco has led to the development of a compostable laminate concept for food packaging to which each partner has given its innovative contribution in terms of raw materials, processing technology, printing machines, coatings, inks and adhesives, offering converters and brand owners a wide range of solutions for the design and manufacturing of flexible packaging. The structure consists of two films provided by Ticinoplast. The first, B100, features extremely innovative properties and is obtained by extruding a new grade of Mater-Bi, a bioplastic by Novamont, a company which has always been active in the development of biodegradable and compostable solutions designed to provide an effective response to environmental issues and to the needs of consumers increasingly aware of the values of sustainability. The film obtained, rigid and highly transparent, incorporates excellent characteristics suitable for the external layer of a compostable laminated structure and printing substrate. For the printing stage, Uteco provided the Diamond HP Model 112 flexographic machine, ideal for large 10-color print runs. The advanced drying unit optimizes evaporation in order to save up to 35% energy.
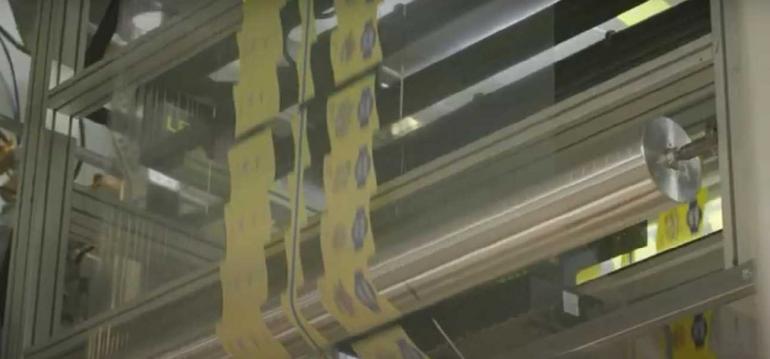
The B100 film - suitable for lacquering and metallization processes to provide barrier properties - is treated with Sun Chemical SunBar BARX 221/222 bi-component coating, which improves the oxygen permeability of the substrate, and then printed with Sun Chemical water-based inks of the Aqualam range, tested and eligible for the OK Compost certificate, and designed for printing lamination substrates at high speeds. Ticinoplast's B102 film was used for the weldable layer, with a particular formulation of Mater-Bi ideal for ensuring higher performance on packaging lines.
The lamination of the B100 and B102 films represents the ideal solution for the production of a compostable laminate which can be used for various applications in the food sector. For products with a short life cycle, Mater-Bi solutions avoid the waste of resources destined to run out and make it possible to reduce the share of unsorted waste in favour of the recovery of resources that, once processed in industrial composting plants, will turn into compost, thus closing the circle of nature where nothing is wasted and everything becomes a resource.
The lamination process is carried out on a Uteco Rainbow 4.0 machine, a highly automated laminating-coating machine designed for meeting the specific requirements of food packaging; the process is performed without the use of solvents at the speed of 500m/min.
Sun Chemical's Solvent Free SunLam SFC 100/HAC 306 compostable adhesive is used for the lamination process. This adhesive features a low monomer content and a high content of renewable resources, which completes Sun Chemical's integrated offer of lamination products dedicated to the production of industrially compostable, sustainable packaging. Recyclability and ecodesign, combined with the stimuli from consumers increasingly oriented to the purchase and consumption of packaged food with less bulky and more sustainable packaging, are changing the food packaging industry, a sector in which the offer of "ready to go" solutions has become a necessity.
Ticinoplast's compostable films feature interesting mechanical properties when compared to traditional PE films such as mLLDPE and LDPE. These films provide excellent welding properties and lower welding temperatures than mLLDPE and LDPE films. In addition, they show radically different behaviors in terms of gas and vapour permeability. These characteristics can be greatly improved through lacquering and metallization. The films in question represent the ideal solution to create compostable packaging.