To ensure that employees and customers are kept abreast of technological innovations, Schubert, a manufacturer of top-loading packaging machines (TLMs), offers training courses at its centre in Crailsheim, Germany, where a new facility has recently been purchased to meet the growing demand for training courses.
In fact, the number of courses has increased over the past year and a half to meet the specific needs of customers and employees. To this end, Schubert has developed new content, designed a series of online courses via a digital platform in addition to face-to-face courses, and hired new staff.
Sarah Busch, Head of Customer Training at Gerhard Schubert, explained:
Our training approach is based on a balanced mix of traditional and digital learning content. Interactive courses and videos are a great way to understand and familiarise yourself with some topics, but it is better to learn some aspects live, in front of the machine with a trainer and a small team, so you can experience reality first hand. Also, as our previous machines were always full, we decided to invest in another model.
From format changeover to troubleshooting - learning on the current model
Exercises carried out on new and old generation packaging machines include standard activities such as robot naming, selecting new programmes on the control panel and their controls, maintenance, identifying and correcting error messages and troubleshooting. The training also covers various system components of the line. From the transmodule to the F2 and T5 robots to the 3D scanner, the aim is to acquire in-depth knowledge.
Sarah Busch added:
The training courses are very much appreciated by both our staff and our customers. With the new training machine, we can expand our capabilities and offer more training courses. Our customers and employees benefit from a hands-on training experience that is useful to everyone in their day-to-day work.
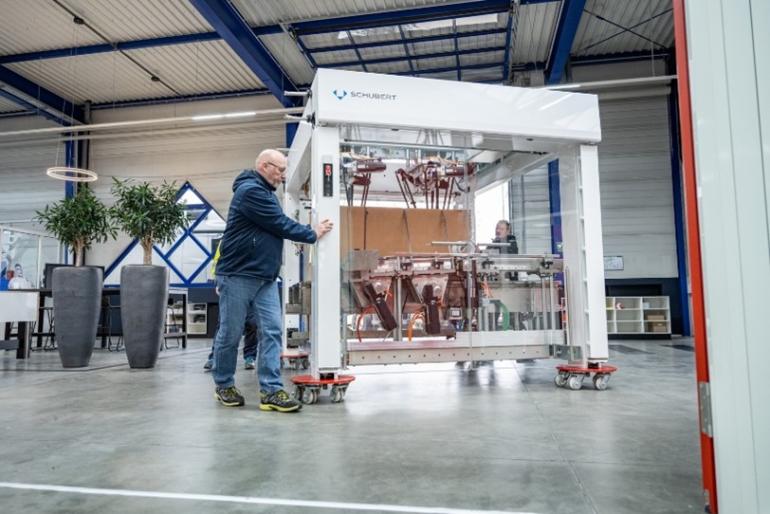