The Finnish start-up H2O4U chooses Robopac to build a “highly sustainable” bottling plant.
The forward-looking intuition of a group of strong international investors has led to the creation of an innovative and eco-sustainable beverage start-up in Finland, H2O4U Finland Ltd, which packages natural spring water of the highest quality. The source is in Lahti - the leading green city in Finland and a leader of environmental work appointed as the European Green Capital 2021. The city has been recognized for its strict regulations for environmental and groundwater protection initiatives.
H2O4U Finland is highly committed to health both for final consumers and for the planet. The company’s mission is to offer LAHQUA®, high quality water in its authentic pure state, and with minimum impact for the environment.
Goal of the project
For that reason, H2O4U Finland reached out to Robopac to participate in a 360° turnkey project targeting at best available technologies - from sourcing to packaging and logistics – to guarantee 100% product quality and safety while using minimum of resources.
Robopac was involved in responding to the need to create a complete end-of-line system to be installed in the green field plant of H2O4U Finland in Lahti, where they are planning the creation of a production site of over 7 thousand square meters. The Finnish company was looking for a collaborator capable of developing a 360-degree “turnkey” project. Robopac fully satisfied this need, proving to be the ideal partner for the study and supply of an integrated end-of-line system with top-range technologies and machinery and supported the customer with highly professional advice for the development of packaging itself. Advice aimed at the different types of water bottling and at the primary input of eco-sustainability.
Focused on evolving trends and consumer needs, H2O4U Finland aims to develop a range of packaging formats suitable for different consumption occasions, with objective to offer convenient and eco-friendly solutions.
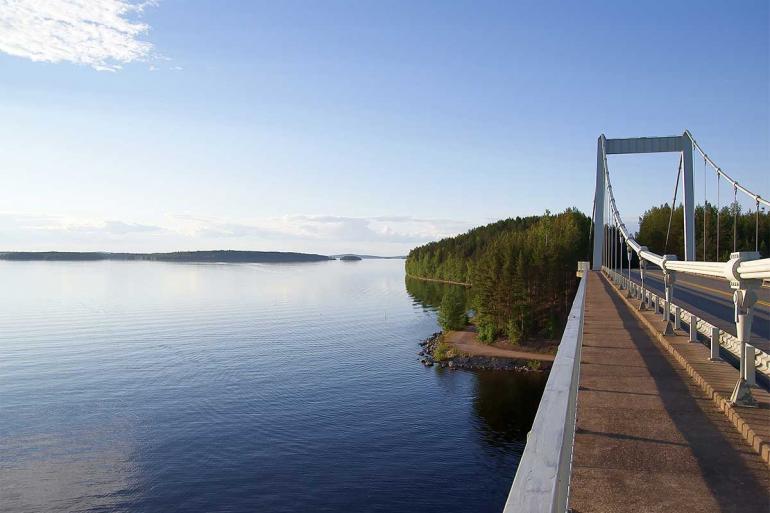
3 types of packaging
At the production level, it translates into the need to study extremely versatile end-of-line solutions for packaging, able to adapt to different materials and formats, and guarantee green technologies that reduce energy and raw material consumption to a minimum.
Automation and flexibility, therefore, were the keywords imposed by the customer on Robopac who studied a tailor-made layout of the structure, optimizing and enhancing the available space. It was also essential to create a plant with a lower environmental impact and that would guarantee reduced consumption. The strong point for the development of the project was the intercompany synergy between Robopac, OCME and the English branch Robopac UK, based in Oakley, collaboration that allowed to identify the ideal choices to satisfy the customer.
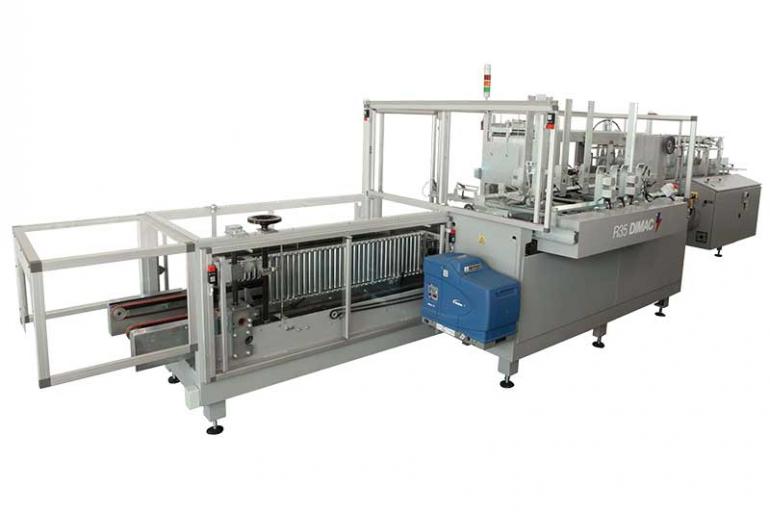
A machine for every need
Robopac has therefore created ad hoc solutions for the different types of products and, overall, has supplied: a STARLINE depalletizer, a Dimac STARWRAP R25 wrap-around case packer, three DYNAMIC PS palletizers, a Prasmatic TCS310W wrap-around case packer, MARIS island robotic palletizing, two GENESIS HS50 automatic ring pallet wrapping machines, aligned to the most advanced needs of Industry 4.0
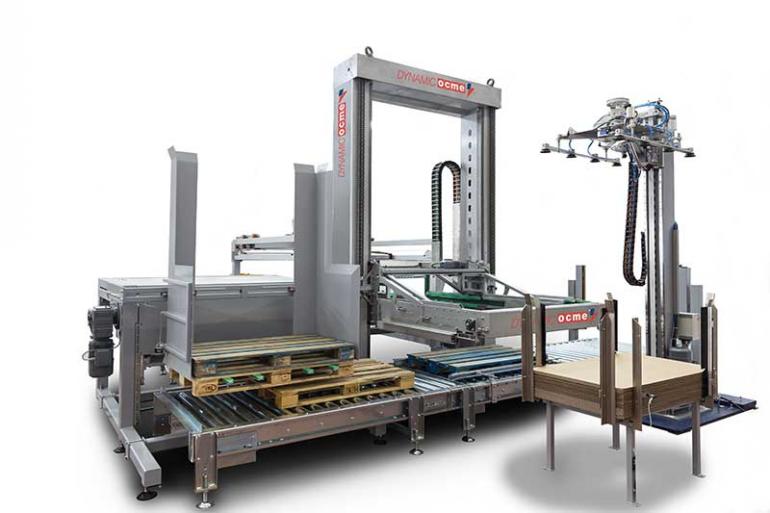
An integrated end of line
Robopac has developed the entire end-of-line system with a view to process integration and automation; in this sense, all the lines convey on a shuttle on rails to the palletizers with exclusive Robopac technology, dedicated to the distribution of empty pallets and the pick-up of full pallets.
This system, depending on the loads, distributes the products on the two Robopac GENESIS HS50, automatic wrapping machine with rotating ring. A distinctive feature of the Genesis HS series wrappers is the exclusive patented system that generates the electricity that feeds the motorized pre-stretch units during the ring rotation. This technical solution allows to operate without sliding electrical contacts, minimizing maintenance costs, eliminating wear problems and allowing the use of the machine even in dusty and humid environments. Genesis HS is also equipped with patented CUBE Technology, which allows to carry out exactly the right amount of film in the exact position with the correct containment force: a further step towards green design, with a view to saving maximum energy and raw material savings.
The plant is completed with a labeling systems perfectly in line with the 4.0 directives of smart factories: the product is traced by the Robopac OCME systems in all its completeness and the data are reported on the label, ensuring maximum transparency and process automation.
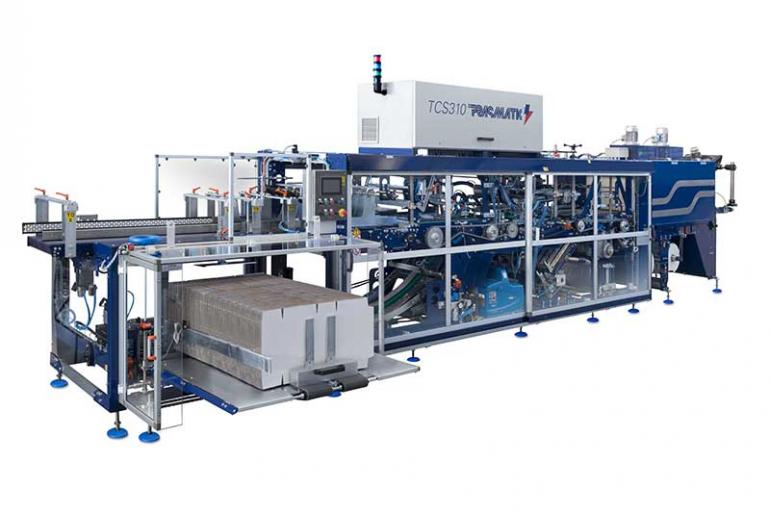
In conclusion
This ambitious project was very stimulating for the whole Robopac and OCME team, which had to resort the best available resources and work in synergy to respond quickly to the customer’s strict deadlines, offering a valid and complete, integrated and “turnkey” solution, that would meet the needs of productivity, efficiency, optimization of costs and raw materials, as well as cutting-edge and green oriented technology.
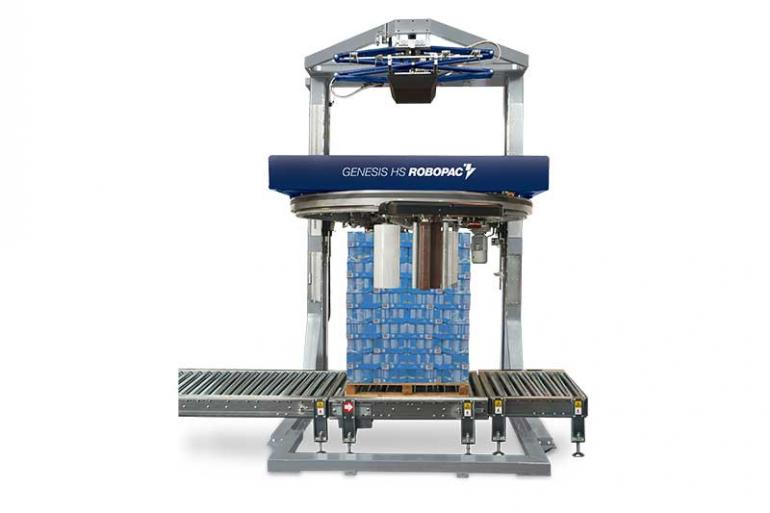