By Giampiero Zazzaro
Improving the current situation of plastic wastes has become a real challenge for society as a whole, involving not only the political and legislative arena but also processing system manufacturers, raw materials processors, recyclers, converters, and consumers. Fortunately, thanks to constant advances in technology, there are enormous possibilities for increasing the recyclability of plastics.
To discuss this topic, an especially hot one in recent years, on the occasion of the Ecomondo fair in Rimini (26-29 October), the editorial department of Packaging Speaks Green organized a brief interview with Alessandro Granziera, Italian commercial manager for Tomra Recycling, a Norwegian company specialized in waste collection, sensor-mediated sorting, and recycling. The company maintains a pioneering role in the sector thanks to its commitment to sustainability.
As part of its development programme for recyclable materials sorting solutions, Tomra Recycling inaugurated a new testing centre in Parma in September dedicated to sorting flakes in the plastics recovery process. Can you tell us what specific operations will be carried out at this facility?
The decision to inaugurate the facility in Parma, located near our Italian plant, represents a typical strategy of Tomra Recycling, that is, to increase investments in the plastics sector, in this case in flake sorting. In particular, we felt it was necessary to expand testing options for our customers, increasing the number of testing centres in Europe (the main one is located in Langenfeld, near Tomra’s German plant). Specifically, as regards the Parma test centre, we decided also to install a number of flake sorting units.
Regarding flake sorting systems, your Innosort Flake and Autosort Flake system have been installed at the new Parma centre. What are their principal technological features, and how do they relate to the material being processed?
Autosort Flake and Innosort Flake are two platforms outfitted with all the options available on the market, making it possible to perform any type of test. As regards polymers it is possible to process PET and polyolefins, thus PE and PP but also PS and PVC. These two plants make it possible to decontaminate materials by polymer type, colour, metal, or all simultaneously. At the same time they are able to work in multi-step configurations. Specifically, some processes might require an initial roughing step in one machine and subsequent processing in another machine in order to ensure that the quality of the material is in line with customer request. Furthermore, I would like to add that it is also possible to start from highly contaminated materials.
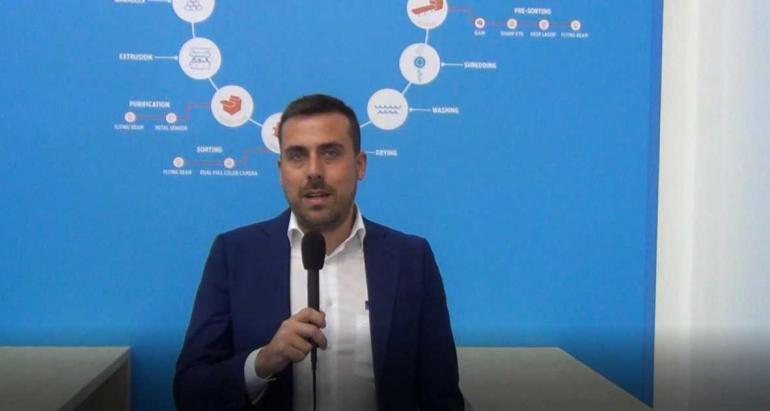
The first edition of GreenPlast will take place from the 3rd to the 6th of May 2022. Can you tell us if you have already registered for the event and how, in your opinion, technologies for the processing of plastics and rubber, and those for recycling in particular, can contribute to ecological transition?
We will be taking an active part in GreenPlast. Let us say that every trade fair - and naturally GreenPlast as well - is important to us because we can meet customers, discuss projects, present our technological innovations, and create a new network of contacts.
As for the ecological transition, Tomra technology is the “brain” of the systems, for both sorting and recycling systems. In both cases our company’s technological solutions involve a large number of machines or subsystems, each with its own specific function.
As regards the identification of the various components in the waste stream and the purification of the material, optical sorting has been and will continue to be one of principal technologies in materials sorting and recycling.
Can you give us a general idea of the state of health of the recycling market in Italy and the world? Is it suffering from a shortage of plastics or does recycling represent a solution here?
In this period, the sorting and recycling market is generally quite healthy. Naturally, there are different drivers of this market, some relating to the cost of materials. Others have to do with legislation in force, not only in Italy but also in other parts of the world. And for about a year now there has also been strong social pressure, with people increasingly concerned with environmental protection, motivated in part by aspects that have a strong emotional impact, such as the situation of plastics in the oceans.
These hot-button issues drive a great deal of interest in technologies for recovering and gaining new value from materials. And I would like to point out that pressure like this, on the social level, has never been seen before.
Because of this social question, brand owners - major consumers of plastics, as well as paper and metal - are beginning to invest more and more in recycling technologies, partly to ensure that their final product can contain an increasingly high percentage of recycled material.
So we can say that there are various drivers, especially legislative, that oblige packaging manufacturers to recover an increasingly large portion of the material going into the final product. And we must also keep in mind that in the future, social pressure may bring new players into the sorting and recycling market.
